Hakkımızda
Küresel ölçekte beklentileri karşılamak adına, vasıflı kalitelerde özel parlak çelikler üretiyoruz.

Güçlü stok yapısı ve yaygın servis merkezlerimizdeki hizmetlerimizle sektör taleplerine anlık çözümler sunuyoruz.
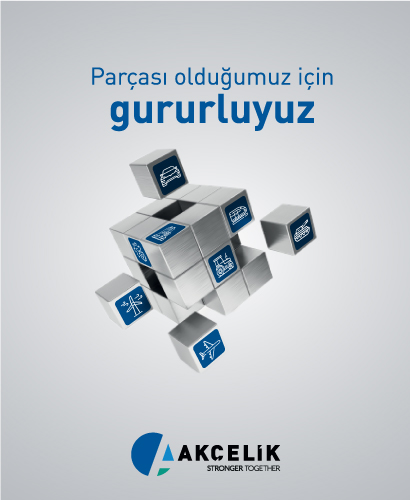
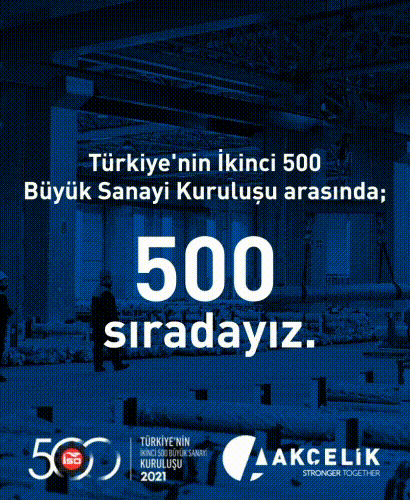
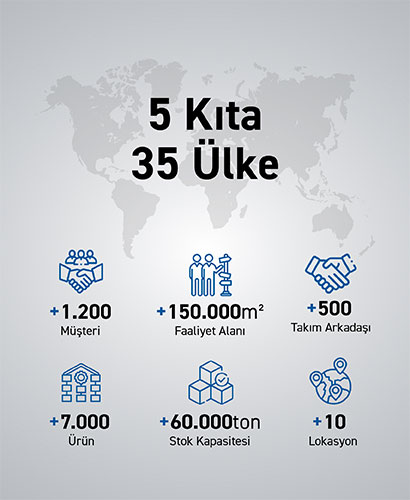
Akçelik Tanıtım Filmi

Vasıflı Çelik Sektöründeki küresel çözüm ortağınız...
Kataloglarımız için tıklayın.
